How to Leverage Data Analytics in Workplace Safety Management Systems for Better DecisionMaking?
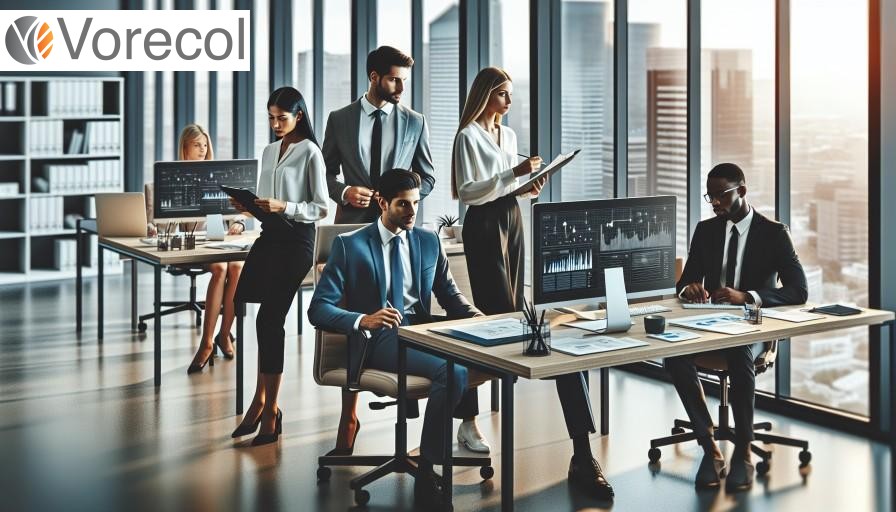
- 1. The Business Case for Data-Driven Workplace Safety
- 2. Key Metrics in Safety Analytics: What Employers Should Track
- 3. Integrating Safety Data with Operational Performance
- 4. Predictive Analytics: Anticipating Risks Before They Occur
- 5. Enhancing Compliance Through Data-Driven Insights
- 6. Case Studies: Successful Implementation of Analytics in Safety Management
- 7. Future Trends in Data Analytics for Workplace Safety Management
- Final Conclusions
1. The Business Case for Data-Driven Workplace Safety
The business case for data-driven workplace safety is becoming increasingly compelling, as organizations realize that safety is not just a regulatory obligation but a strategic advantage. A report from the National Safety Council indicates that companies with robust safety programs can achieve up to a 40% reduction in injury-related costs. For instance, the multinational construction firm Skanska adopted advanced data analytics tools that allow them to predict potential hazards on job sites based on historical incident data. By leveraging these insights, they were able to implement preventative measures, resulting in a remarkable 30% decrease in accidents over three years. Imagine viewing your workplace safety strategy through a high-tech lens where data illuminates the hidden risks—this approach can transform how businesses think about safety and ultimately drive profitability.
Organizations must ask themselves: Can your workplace become a safer environment simply by transforming data into actionable insights? As seen with Dow Chemical, which integrated a sophisticated data analytics system to monitor their operations, they not only enhanced safety but also increased operational efficiency by 15% in just one year. This case illustrates how data can serve as a powerful compass guiding decision-makers toward safer practices. For leaders seeking to enhance their safety management systems, it's essential to invest in technology that consolidates data from various sources—like IoT sensors and employee feedback—into a cohesive framework. This holistic approach not only mitigates risks but also cultivates a culture of safety that resonates through every level of the organization. Are you ready to watch your safety numbers soar by embracing a data-driven mindset?
2. Key Metrics in Safety Analytics: What Employers Should Track
In the realm of safety analytics, key metrics serve as vital navigational tools, aiding employers in steering their workplace safety strategies effectively. Employers should meticulously track incident rates, near-miss reports, and safety training completion rates. For instance, consider the case of a manufacturing firm that diligently recorded near-miss incidents and found that addressing these early warnings led to a dramatic 30% reduction in workplace accidents over the course of a year. This highlights the importance of not just focusing on injuries but also on near-misses, akin to a ship captain monitoring weather patterns to prevent storms rather than just navigating through rough seas. Employing dashboards that visualize these metrics can aid decision-makers in identifying trends and adjusting their safety protocols proactively.
Moreover, evaluating employee engagement in safety programs is crucial. Metrics such as employee safety perception scores and participation rates in safety drills can provide insights into the overall safety culture of an organization. Take the example of a construction company that implemented a safety suggestion program; their data showed a 50% uptick in anonymous submissions within just three months, leading to actionable changes on-site. This phenomenon is reminiscent of harnessing the quiet power of whispers in a bustling crowd. By actively inviting feedback and tracking these metrics, employers can cultivate an environment where safety is a shared responsibility, ultimately leading to more informed decision-making and safer workplaces. Implementing regular reviews of these key metrics ensures that safety management systems are not static but evolve in alignment with the changing dynamics of work environments.
3. Integrating Safety Data with Operational Performance
Integrating safety data with operational performance is akin to assembling the vital pieces of a jigsaw puzzle, where each piece represents critical insights into workplace dynamics. For instance, companies like DuPont have effectively combined safety metrics with production data, resulting in a staggering 64% reduction in injury rates over the past decade. By harnessing analytics that correlate safety incidents with operational conditions, organizations can unearth patterns that reveal how specific operational practices may contribute to risk exposure. How can leaders ensure that their operational decisions do not inadvertently compromise safety? The answer lies in leveraging integrated data to create a holistic view of workplace dynamics.
Employers should adopt a data-driven decision-making approach by establishing key performance indicators (KPIs) that encompass both safety and operational efficiency. For instance, the construction firm Bechtel has utilized this methodology to reduce costs while improving safety outcomes, achieving a 30% improvement in project delivery timelines without compromising safety standards. To replicate such success, organizations can begin by developing dashboards that visualize safety trends alongside operational performance metrics, fostering a proactive culture of risk management. By asking not only "What happened?" but "Why did it happen?" companies can turn data insights into actionable strategies, creating systems that resonate with both the heart of your workforce and the company's bottom line.
4. Predictive Analytics: Anticipating Risks Before They Occur
Predictive analytics serves as the crystal ball of workplace safety management systems, enabling employers to foresee potential risks before they escalate into incidents. By analyzing historical data trends, companies can identify patterns related to injuries, equipment failures, or near-miss events. For instance, companies like Boeing have implemented predictive models that analyze maintenance logs, employee behavior, and environmental conditions, resulting in a 20% reduction in workplace accidents. Imagine the opportunity to turn historical data into proactive measures—what if employers could predict a potential slip-and-fall incident before it even occurs? This not only mitigates risks but also fosters a culture of safety awareness and continuous improvement within the organization.
Employers can enhance their safety management systems by integrating predictive analytics tools that utilize machine learning algorithms to detect anomalies in operational processes. For example, in the manufacturing sector, General Electric adopted predictive maintenance strategies that rely on data from sensors monitoring equipment health, reducing machinery-related incidents by 30%. As such, it is vital for organizations to establish a robust data collection framework and leverage visualization tools that translate complex datasets into actionable insights. By asking the right questions—Are we tracking the right metrics? How can these predictions guide our safety protocols?—employers can create a safer workplace environment while simultaneously optimizing operational efficiencies. Ultimately, the application of predictive analytics transforms data from mere numbers into a strategic compass guiding decision-making towards safety and sustainability.
5. Enhancing Compliance Through Data-Driven Insights
Data-driven insights have revolutionized compliance in workplace safety management systems, enabling employers to proactively identify potential risks and behaviors that could lead to accidents. For instance, a leading construction company, Turner Construction, implemented an analytics platform that aggregated data from incident reports, safety audits, and employee training sessions. By analyzing this data, they uncovered patterns linking specific job sites with higher accident rates. With this insight, they enhanced their compliance protocols—establishing stricter safety measures in identified high-risk areas, resulting in a 30% decrease in incidents. In this era of big data, companies must ask themselves: how well do we understand the safety landscape of our operations?
Employers can harness the power of data analytics not just for monitoring compliance, but also for fostering a culture of safety. For example, the health care giant Kaiser Permanente utilized predictive analytics to preemptively address workplace hazards. By correlating data from employee feedback and incident reports, they identified stress-related injuries as a significant issue. This prompted a company-wide initiative to implement wellness programs, drastically improving staff morale and consequently reducing workplace injuries by over 25%. Employers should consider conducting regular data audits to uncover hidden insights, enabling them to tailor safety programs to better fit their workforce. As the adage goes, "What gets measured gets managed"—and in the realm of workplace safety, this could mean the difference between a proactive or reactive approach to compliance.
6. Case Studies: Successful Implementation of Analytics in Safety Management
One striking example of successful analytics implementation in safety management comes from the manufacturing giant, General Electric (GE). By deploying predictive analytics tools within their operations, GE reduced workplace incidents by approximately 20% within the first year of implementation. This transformation can be likened to upgrading from a standard light bulb to a smart system that not only illuminates but also adjusts according to surrounding conditions. GE utilized data from past incidents, near misses, and employee feedback to identify risk patterns, enabling them to proactively address hazards before incidents occurred, thus fostering a culture of safety that resonates throughout the organization. Isn’t it intriguing how data can act as a crystal ball, revealing potential dangers long before they manifest?
Similarly, the mining industry has witnessed notable advancements through data analytics, particularly in companies like Rio Tinto. By leveraging IoT devices and real-time analytics, Rio Tinto enhanced their safety protocols, resulting in a remarkable 40% reduction in safety incidents over just three years. Just imagine the difference between navigating a dark, uncharted forest versus having a detailed map guiding your path; Rio Tinto’s data-driven strategies serve a similar purpose in safety management. To employers looking to replicate such success, it is advisable to invest in an integrated data analytics platform that not only compiles reports but also visually highlights trends and anomalies. By doing so, organizations can transform their safety strategies from reactive to proactive, ultimately safeguarding not only their employees but also their bottom line.
7. Future Trends in Data Analytics for Workplace Safety Management
As workplace safety management evolves, future trends in data analytics are poised to redefine how organizations approach risk mitigation. With the advent of advanced machine learning algorithms and real-time data collection through IoT devices, businesses can now predict potential safety incidents before they occur, similar to how meteorologists forecast storms. For instance, a construction firm leveraged predictive analytics to analyze data from past incidents, leading to a 30% reduction in on-site accidents over two years. This proactive approach not only enhances employee safety but also saves companies significant costs associated with injuries and downtime, reinforcing the critical question: could data analytics be the new compass guiding employers through the often-turbulent waters of workplace safety?
Moreover, the integration of artificial intelligence and big data analytics is set to transform compliance monitoring and reporting processes. Organizations like Boeing have implemented these technologies to analyze vast amounts of operational data, ensuring adherence to safety regulations without the manual burden on teams. As companies move towards a more data-centric environment, it is vital they harness these tools effectively. Employers should consider investing in comprehensive training programs that facilitate a data-driven culture within their organizations. As with any new technology, the key to success lies in not just the tools themselves but in empowering employees to interact with data and derive actionable insights. How prepared is your organization to embrace this data revolution for safety management?
Final Conclusions
In conclusion, leveraging data analytics in workplace safety management systems significantly enhances decision-making processes by providing actionable insights derived from real-time data. By integrating advanced analytics tools, organizations can identify patterns, predict potential hazards, and assess the effectiveness of safety protocols more efficiently. This proactive approach not only minimizes workplace accidents but also fosters a culture of safety, encouraging employees to engage actively in safety measures. As a result, companies can make more informed decisions that not only safeguard their workforce but also contribute to overall operational efficiency and productivity.
Furthermore, as industries evolve and the volume of available data continues to grow, the importance of data-driven safety management will only increase. Organizations that invest in robust analytics capabilities will be better equipped to adapt to changing regulations, employee needs, and emerging risks. By continuously monitoring and analyzing safety data, businesses can refine their strategies and develop tailored interventions that address specific challenges. Ultimately, the utilization of data analytics in workplace safety management is not merely a trend, but a vital component for sustainable growth and employee well-being in the modern workplace.
Publication Date: November 29, 2024
Author: Psico-smart Editorial Team.
Note: This article was generated with the assistance of artificial intelligence, under the supervision and editing of our editorial team.
💡 Would you like to implement this in your company?
With our system you can apply these best practices automatically and professionally.
Work Environment - Climate Assessment
- ✓ Measure and improve your work climate
- ✓ Detailed surveys + comparative analysis
✓ No credit card ✓ 5-minute setup ✓ Support in English
💬 Leave your comment
Your opinion is important to us